Aeronautics pilot: advanced CFD simulations of aeronautical engine critical parts
The aeronautics large-scale pilot aims to significantly enhance the feasibility and exploitation of advanced Computational Fluid Dynamics (CFD) numerical modelling capabilities able to predict the fluid-dynamic behaviour of aircraft engine critical components. To meet this ambitious objective, the industrial applicability of the next generation HPC/cloud/big data management technologies is assessed in LEXIS through two aeronautical engineering case studies, a turbomachinery application, and a mechanical rotating part.
Faster and more accurate CAE analyses, that exploit newly deployed HW/SW resources in the LEXIS engineering platform, are carried out to enable the implementation of the improved or newly designed CFD-based engineering methodologies that both considered case studies rely on.
Aeronautics turbomachinery use case
Referring to the aeronautics turbomachinery use case, a high-level overview of the deployed CFD simulation process is depicted in the following figure that illustrates the three main stages (preprocessing, analysis solver execution, postprocessing of results) of the application workflow.
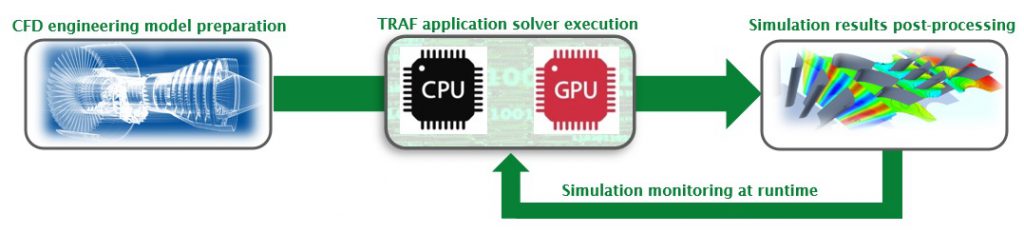
Based on TRAF code, a CFD solver developed by the University of Florence is used to investigate fluid dynamics phenomena with a special focus on turbomachinery simulations. The computational phase is here strongly HPC-demanding and time-consuming. In order to drastically reduce the execution time of TRAF-based fluid dynamics analyses on low-pressure turbines, a newly designed GPU-enabled solver release has been developed, showing promising results in terms of speed up. The considered turbomachinery pilot test case is representative of a multi-stage turbine, shown in the following figure.
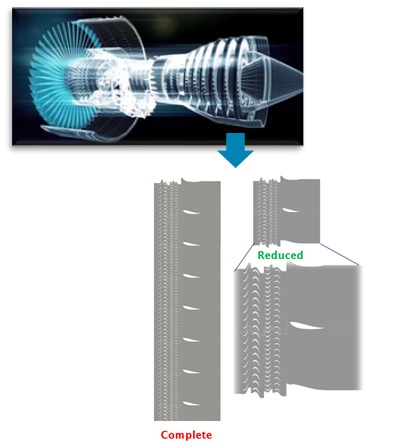
Due to a large number of computational blocks, the underlying CFD model is very HW-intensive in terms of both the required memory resources and the execution time needed to perform the calculations. Since the memory in the currently available GPU accelerated systems is not sufficient to manage this model, a reduced version of the test case has been used (see the figure above).
The shown representations of the test turbine are marked as “Complete” and “Reduced” depending upon whether a pure CPU-based system or a GPU-equipped system is used respectively. Compared to the solely CPU-based system, the CFD simulations executed through the GPU-ported release are currently running 5.22x faster on the Barbora HPC. Although the basic industrial target in terms of simulation speed-up has been reached, the research team within the turbomachinery use case foresees further optimisations for the computational phase, looking to take advantage of the latest compiler enhancements to minimise remaining performance bottlenecks and to exploit the best GPU-to-GPU communication channels. Moreover, the opportunity to further reduce the execution time of the most HW-intensive subroutine of the CFD solver through FPGA-based HPC platforms is investigated.
The rotating parts use case
As regards the rotating parts use case, a high-level overview of the deployed CFD workflow is depicted in the following figure which illustrates its three main computational stages and the involved key software applications. Based on ALTAIR nanoFluidXTM, a smoothed particle-based hydrodynamics (SPH) simulation tool conceived and optimised for use on clusters of GPUs to predict multi-phase flows around complex geometries under complicated motion, the computational phase here is also strongly HW-intensive and requires advanced HPC systems equipped with several GPUs due to the complexity of the input models. With the aim of tuning a new CFD-based engineering practice to simulate, the flow field operates the multiphase flow inside gearboxes with increasing accuracy. The presented application workflow is being deployed over the 3 engineering case studies, differing in their degree of complexity and sensitivity.
The three considered rotating parts test cases are:
• single high-speed wheel used to run separately SPH Oil Phase simulations and airflow,
• gear pair with oil jet lubrication adopted with the target of applying the multi-phase approach in simplest gearing geometries,
• planetary gearbox selected to carry out and validate industrial-like simulation predictions on a more complex environment, illustrated in the lowest figure of this page.
Based on the preliminary outcomes from the research activity within the rotating parts use case, the first phase of investigation can be considered accomplished. SPH methodology is really promising with reference to the pre-processing phase, simple and very short, despite alternative CFD methods, like Finite Volume numerical which requires longer simulations (about 10x more time-consuming). Finally, some best practices to carry out air/oil investigation have been defined with very good agreement with experimental data.

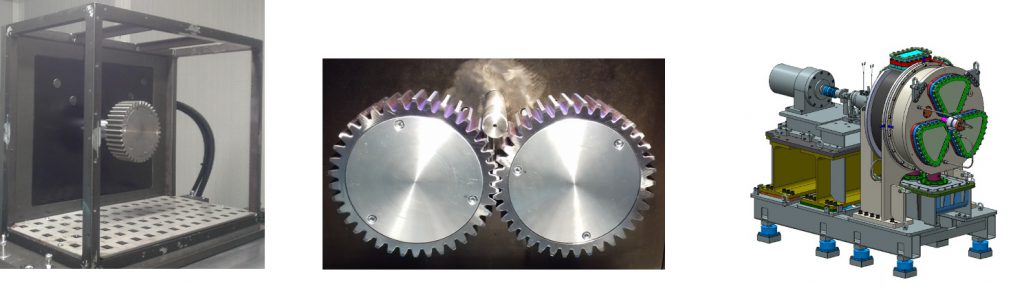